Small Home Gazette, Spring 2020
Tiffany Lamps
One Woman’s Experience at Making Her Own Shade
Tiffany Studios began fabricating its famous leaded-glass lamp shades with nature-inspired themes in 1885, the majority made between 1895 and 1920. The lamps started as small versions of Louis Comfort Tiffany’s elaborate stained glass window designs before growing into a collection of stocked works of art for the wealthy. In 1902, the complex Wisteria-design lamp shades sold for $350 each, or $10,400 in today’s dollars.
An original Tiffany table lamp can still cost a pretty penny. At auction, poinsettia motif table lamps have sold for up to $52,000. If those prices are out of your range, you can commission a high-quality reproduction from Century Studios in St. Paul for a fraction of the cost.
Or, you can make your own. After all, according to one stained glass supply company’s blog, “Thanks to a wide assortment of patterns, molds and instructions, it’s easy for hobbyists to make Tiffany-style lampshades.”
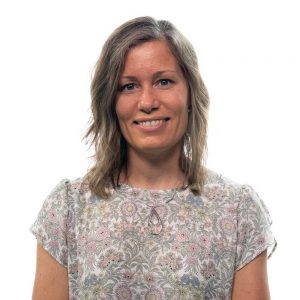
Stained glass hobbyist Karen Swoverland.
Easy?
After completing two Tiffany table lamps, my friend Karen Swoverland will tell you otherwise. She will tell you that every stained-glass lamp requires hundreds of hours of painstaking, obsessive work. Her first Tiffany lamp was a 435-piece Azalea 10-inch shade, completed during an eight-week studio class. Inspired by her success, she immediately launched into a 16-inch diameter Poinsettia design shade, which stretched into a five-year project, completed in fits and starts.
Each step in the process requires an eye for design; skills developed through experience; a serious investment of time; and patience—lots and lots of focused patience. Frustrated and tired partway through her solo second lamp project, Karen set it aside. A few years later, she unearthed it and took a class at Glass Endeavors, located in Minneapolis, both as a technical refresher and to structure her progress. Several other students in the class were taking it for a second time as well.
If you missed the Bungalow Club’s 2009 event featuring Century Studios’ demonstration of stained-glass lamp making, the below steps—spiced with snippets of Tiffany history and details from Karen’s experience—should convey a sense of what is involved.
Select a Form
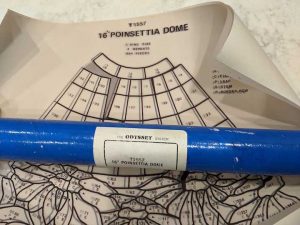
Pattern for an Odyssey Lamp Systems poinsettia shade.
Design options for Tiffany-style lamps abound: geometric or botanical; cone or globe shaped; smooth or irregular borders. The Odyssey Lamp System collection, based in California, has more than 100 fiberglass forms, or molds, to choose from, ranging from 4½- to 28-inch diameter shades. Its numerous Tiffany designs include the famous Daffodil, Dragonfly, and Wisteria. Tiffany Studios employee Clara Driscoll is credited with creating these and many other designs, following the company’s tradition of nature-inspired themes.
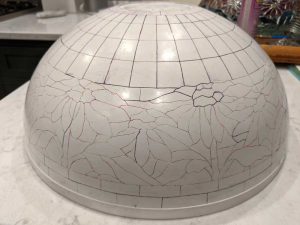
Dome mold for Karen’s poinsettia shade.
My friend Karen’s choice, the 16- inch Poinsettia lamp shade, has 664 pieces, with four repeated pattern sections. A more obsessive crafter might choose the 22-inch Laburnum pattern of hanging flower clusters, with 1,986 pieces.
Select the Glass
Tiffany’s artistic medium was glass. Unlike his contemporaries who were painting on glass, Tiffany was motivated by the ideals of the Arts & Crafts movement and sought fidelity in his art. A collector of ancient glass, he found truth and beauty in its imperfect nature. “Rich tones are due in part to the use of pot metal full of impurities,” he said, “and in part to the uneven thickness of the glass.” Building from ancient glassmaking techniques, he patented Favrile glass, an opalescent glass produced when several colors are combined and manipulated to create a range of hues and three-dimensional effects.
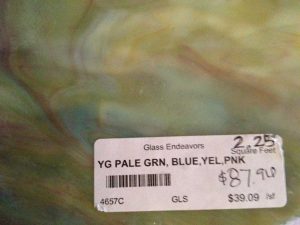
Label on a sheet of multicolored stained glass.
Karen’s lamp-making class included color theory. Colors can complement or contrast; they can make design elements appear to advance or recede, as if some flower petals are in the foreground and some in the background. Karen made several copies of her paper pattern and used colored pencils to choose the general color scheme for her lamp. Following the ethos of Tiffany, she selected handmade art glass, which offers a rich diversity of color and texture in one sheet. Consequently, her lamp’s shades of red, blue, green and yellow came from two large sheets of glass.
One happy circumstance of setting her project aside for a time is that Karen reconsidered her original color selections for the flower petals. This prevented what might have ultimately looked like groups of pink and white candy canes instead of rich-toned poinsettias.
Illuminated glass can look dramatically different from unlit. Some areas of Karen’s finished lampshade look green with tints of pink when the lamp is on, but milky blue when off. Karen used a light box to illuminate the glass sheets to select the specific color and texture for each piece of the pattern. Once pieces were cut, she laid them on a flat, translucent mylar pattern on the light box to confirm the overall look of the shade.
Cut, Grind and Foil
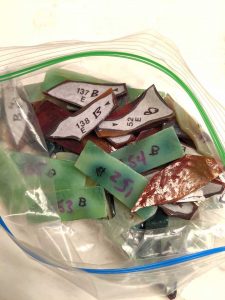
Cut and labeled pieces of glass, ready for grinding into final form.
Each piece of glass needs to be cut from the sheet using specialized tools. Karen labeled each of the 664 pieces to keep track of which side faced out and its specific location within each of the four repeating design sections. She ground the edges of each piece smooth using a water grinder but then discovered she had cut every single piece too large. The thought of regrinding hundreds of pieces caused her to shelve the project for years. When she resurrected it, Karen did what she had to do—resize and smooth the edges of each piece for a second time.
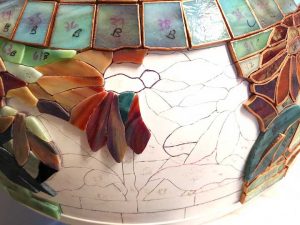
Fitting the finished glass pieces onto the mold
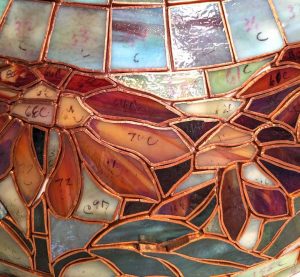
The edges of each piece of glass are wrapped in copper foil and affixed to the form with wax.
Karen, using a technique developed by Tiffany, first wrapped the edges of each glass piece in foil before fixing them onto the dome mold with wax. Tiffany’s use of foil instead of the heavy lead channels traditionally used by glass crafters allowed him to create designs with a level of detail never before possible.
Soldering the glass pieces together is done in three stages. First is “tinning the shade.” This involves tacking the glass pieces to each other with small quantities of solder. Karen started this process, then took a five-month break.
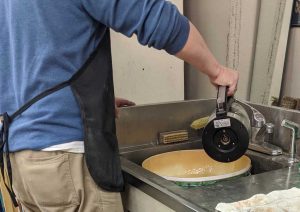
Hot water is poured into the form, softening the wax to release the shade from the form.
Upon the project’s second resurrection, Karen needed to remove the shade from the mold. This required a utility sink large enough to submerge the entire unit in warm water to soften the wax and flex the fiberglass mold to release the shade. Lacking a utility sink and fearful of breaking the solder tacks, Karen chose to pay a modest studio fee of $12 an hour at a stained glass shop to access tools and expert assistance.
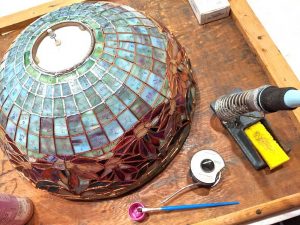
Soldering tools: a brush for applying flux; a spool of solder; and an electric soldering gun.
The second phase of soldering is to create a tidy bead of solder in each channel between every glass piece on the inside of the shade. This step took Karen about eight hours. The work had to be precise, as the inside solder can be seen from a vantage point below the finished lamp, or even through the lit shade. Another eight hours was needed for the final phase—meticulously soldering the channels on the outside of the shade.
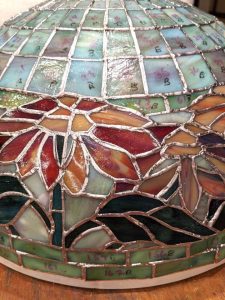
Solder has been applied between each piece of glass, on top of the copper foil-wrapped edges.
Glass grinding and soldering are physically taxing. Karen spent long hours bent over her work, often balancing the form while soldering.
Choose a Base and Finish the Solder
A Tiffany lamp base is a work of art and a key part of a lamp’s design. Original Tiffany lamps were made with a heavy ring of lead inside a hollow bronze base and sometimes had enamel or mosaic ornamentation. Less frequently they were made of art pottery. A wide variety of reproduction Tiffany lamp bases are available. Most lamp bases can be purchased shade-ready, no wiring or finishing needed, with a finial or ventilated heat cap at the top. Karen chose a brass base with a bronze finish and two bulb sockets with pull-cords.
Karen said the lamp-making process did, at least, have one quick and easy step—applying a patina to the solder. Patina options include black, copper, green, or a blend of those colors. Karen chose black to complement the base and bring out the depth of glass colors. She applied it to the shade’s channels, scrubbing it into all crevices using a toothbrush.
Illuminate and Enjoy
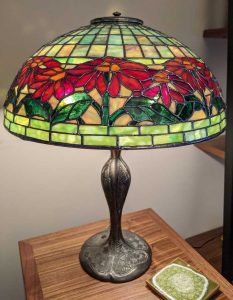
Karen Swoverland’s completed lamp.
According to Century Studios, production time to complete a single shade can take 30 to 300 hours, depending on the complexity of the design. Karen cannot tell you how many hours went into her lamp. With more practice, though, she might gain the skill and speed of a “Tiffany girl” shade maker from a century ago. For now, until she forgets the labor and frustrations, she is content to bask in the glow of her personal masterpiece.
Whether you purchase a lamp or tackle building your own, a lamp crafted with Tiffany techniques is truly a work of art.
Resources
-
Century Studios, 1816 St. Clair Ave., St. Paul.
Rack of glass and molds. Photo courtesy Century Studios.
See how a lamp is made
- Glass Endeavors, 2716 East 31st St., Minneapolis.
Nine-session course available
- “2010 Odyssey Catalog”
Forms/molds and bases for reproduction Tiffany lamps
- A New Light on Tiffany: Clara Driscoll and the Tiffany Girls, Eidelberg, Martin P., 2007.
Book focuses on the 27 women who labored behind the scenes to create the masterpieces now inextricably linked to the Tiffany name.